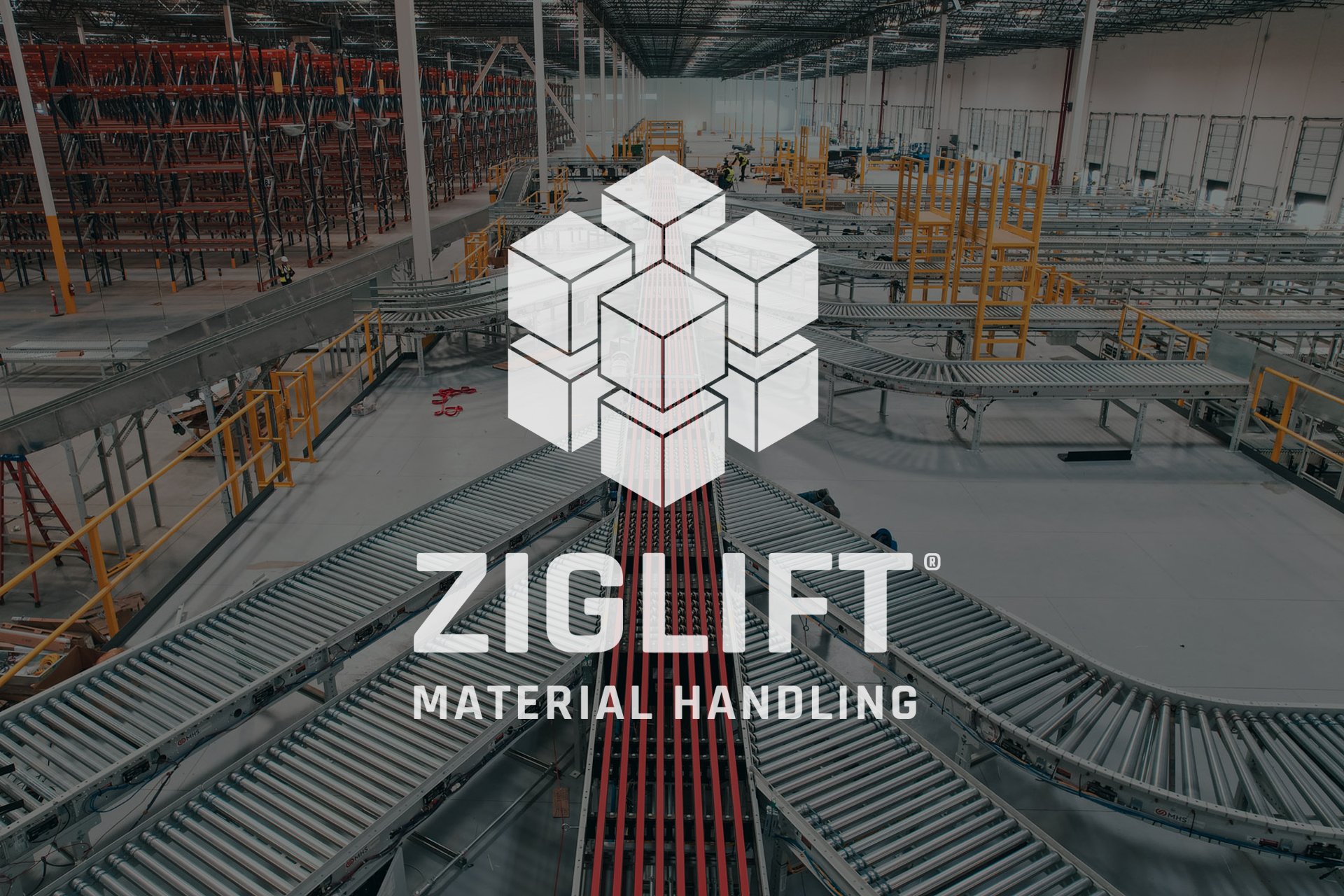
The Power of Conveyor Sortation Systems in Warehouse Automation
In today’s fast-paced world of e-commerce, warehouse automation has become a critical component for businesses striving to meet the growing demands of customers. One essential aspect of warehouse automation is the use of conveyor sortation systems.
What are conveyor sortation systems?
Conveyor sortation systems are advanced technology solutions designed to streamline and optimize order fulfillment processes within a warehouse environment. These systems automate the movement of products, enabling quick and accurate sorting, routing, and distribution.
How do conveyor sortation systems work?
Conveyor sortation systems consist of a network of conveyors that transport items through different stages of the sorting process. As products move along the conveyor, they are identified and sorted according to predefined criteria, such as destination, size, weight, or SKU.
There are several types of conveyors:
- Gravity Conveyor – This type of conveyor uses the power of gravity to move packages along the fulfillment line. They are height-adjustable to create a slight decline along the line to allow packages to flow along rollers or skate wheels. They are ideal for moving lightweight cartons, trays, or totes short distances in a facility.
- Powered Conveyor – These systems function with a mechanical device that moves products and materials along a conveyor line. There are two types of powered conveyors: roller and belt conveyors.
- Motorized Driven Roller Conveyor (MDR) – These conveyors use a chain or belt driven by multiple smaller, low-voltage motors. MDR conveyors are a more efficient and greener solution than high-voltage motor-driven conveyors. They facilitate smooth product accumulation, require minimal maintenance, and achieve high throughput rates.
- Vertical Reciprocating Conveyors (VRCs) – These conveyors are typically utilized in facilities with multiple levels of storage where materials need to flow up or down vertically depending on picking or replenishment activities. They offer material lift efficiencies by providing quick conveyance of products from mezzanines, pick modules, and other multiple-level environments.
- Conveyor Sortation – This type of conveyor system involves identifying products on a line and redirecting the item to a specific location based on a set of criteria. In high-volume distribution centers, automated sortation solutions can be added to conveyors to support quicker and more accurate fulfillment.
When considering diverse perspectives, it is important to keep in mind that not all conveyors may be suitable for all types of products or facilities. Additionally, some conveyors may require more maintenance or have higher energy consumption than others, which could impact the environment. Finally, it is important to ensure that conveyors are designed and implemented with safety in mind to avoid any potential accidents or injuries in the workplace.
Various technologies are employed in conveyor sortation systems. For instance, barcode scanners, RFID tags, and vision systems are used to capture data about each item. This data is then used to determine the appropriate sorting destination for the product.
Once sorted, the items are directed down specific lanes or chutes, leading them to the appropriate dock door or distribution area for further processing. The entire process happens seamlessly, ensuring efficient order fulfillment.
Benefits of conveyor sortation systems
- Increased throughput: Conveyor sortation systems enable warehouses to handle high volumes of products quickly and efficiently. By automating the sorting process, warehouses can speed up order fulfillment, reducing lead times and improving customer satisfaction.
- Accuracy: Manual sorting processes are often prone to errors. Conveyor sortation systems eliminate these errors by ensuring accurate identification, sorting, and routing of products. This helps minimize order inaccuracies and reduces the risk of shipping errors.
- Flexibility: Conveyor sortation systems offer modular designs that can be easily customized to suit the specific needs of a warehouse. Whether it’s handling different product sizes, weights, or packaging types, the system can be tailored to meet the unique requirements of the operation.
- Space optimization: By utilizing vertical space and compact designs, conveyor sortation systems help warehouses make the most efficient use of their available space. This is especially beneficial in urban areas where warehouse real estate is limited.
- Improved labor productivity: With automated sorting systems, warehouse staff can focus on more value-added tasks instead of manual sorting. This leads to increased labor productivity and allows employees to work on more complex operations.
- Real-time tracking and traceability: Conveyor sortation systems integrate with warehouse management systems, providing real-time visibility into the status and location of each product. This enhances inventory control and allows for better tracking and traceability, reducing the risk of lost items.
Conclusion
Conveyor sortation systems have revolutionized warehouse automation by streamlining order fulfillment processes. Offering increased throughput, accuracy, flexibility, space optimization, improved labor productivity, and real-time tracking, these systems have become essential tools for businesses aiming to meet the demands of a rapidly evolving market. Investing in conveyor sortation systems can help warehouses achieve operational excellence, enhance customer satisfaction, and stay ahead of the competition in the ever-growing world of e-commerce.
Contact Us
Let's talk about your next project!
Give us a call at 1 (562) 407-5438 or email us: web@ziglift.com